4 Common Issues with Print and Apply Labels
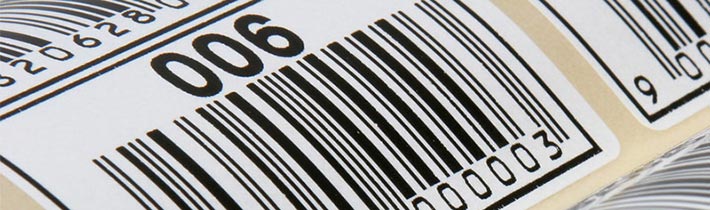
Like any other form of technology, automated print-and-apply label applicators are not perfect. Occasionally labels are dispensed with a low quality print or labels may not apply correctly to the product. Often times there are simple solutions or easy fixes to these problems that don’t require a lot of time or maintenance to solve.
Labels are curling up
This problem happens most often with longer labels – specifically, labels over 5 in. long. As you get closer to the core of the roll, you may notice that some of the labels curl at the ends and are nearly impossible to apply correctly. It’s a really frustrating problem, and you may think that
- The label printer applicator vacuum system that holds the label on the applicator pad is broken.
- The adhesive you are using is not of great quality.
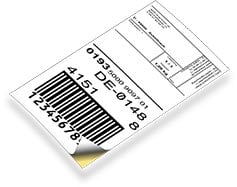
If you are hand-applying the labels, you may try to remedy the problem by peeling the label from the liner in a different direction. We usually peel labels from one end of the label to the other – try peeling from top to bottom. If that doesn’t work, your problem lies in the core diameter of your roll of labels. Labels typically come on a 3in. core diameter roll, but if your label is 5in. or longer, you may need to use a larger core diameter in order to remedy the curling.
Labels won’t peel off the liner
There are several reasons why your label is either difficult to remove from the liner or impossible to peel. Check first to see if there is an issue with your die strike. Test your die strike by outlining the die cutting area with a marker. If it results in a solid black line along the die cut, your die strike is cutting too deep – if you see “legs” your die strike isn’t cutting through the adhesive completely.
Another common cause of labels that are difficult or impossible to peel may be the result of stiffening in the label liner. Either the liner you are using is too thick for the print-and-apply label applicator’s peel bar – the part of the applicator that removes the label from the liner before applying it to the product – or the liner is too thin.
Labels/Barcodes have a poor print quality
It’s very important to maintain a high-quality of print when printing labels, and especially when printing barcodes. Labels and barcodes both contain important information about the product that needs to be legible and clearly printed for the customer, supplier, and others who come in contact with the product to see. Barcodes in particular must be verified before your product is sent out – if it is not verified or if there is a problem with the quality of the barcode, you can lose a lot of money and product.
Poor print quality could be the symptom of several problems that are easily remedied. If you notice that the quality of print on your labels is below what is expected, first check your print head heat settings. Check the heat setting of your print head as well as the pressure being applied. Having an incorrect heat setting or an incorrect amount of pressure can result in a few different defects in the print quality of your label or barcode. If you are noticing wrinkles or lines in your labels or barcodes, the ribbon or the label material may be inserted into the machine incorrectly, or the material is not taut enough when the ink is being applied. If you are having problems with “fuzzy edges,” it could prevent the barcode from being properly read. Be sure you are using quality materials and the correct combination of materials when printing your barcodes.
If none of those solutions improve the quality of the print on your labels, it’s likely that your print head has not been cleaned properly. It’s important that you ensure your print head is cleaned at the end of each day. Dirt build up on the print head is one of the most common causes of poor print quality. Instruct your operators on the proper cleaning techniques and stress the importance on maintaining a clean print head.
Labels are peeling off of products in certain environmental conditions
You may want to apply labels that are easily removed to products such as drinking glasses or home décor, but there are certain products that require a label to remain fixed for safety reasons. In these cases, it’s important that the label can withstand certain environmental elements. For instance, it would need to withstand extreme heat or excessive amounts of water.
If you are manufacturing a product that requires a label to remain on the item for a long period of time without peeling or fading, you need to be careful in choosing the type of label. You also need to be cautious about the type of ribbon you are using – an Ultra Durable resin ribbon is extremely effective in different environmental conditions. Before assuming there is a mechanical issue with your print-and-apply solution, be sure you are using the appropriate supplies to make and adhere your labels.