Case Study: Standardizing Label Application System Company Wide
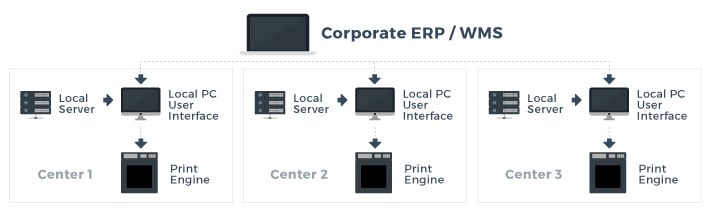
It’s not uncommon for packaging and labeling process problems to occur within organizations that have multiple locations. When clients approach LabelPack Automation with this concern, our first question is, “Do you have a standardized labeling process throughout your organization?”
Most often, the answer is no.
Having a Standardized Labeling Process minimizes waste while improving labeling quality and accuracy. For companies with multiple locations, LPA always suggests creating a Standardized Labeling Process to uphold print quality and labeling accuracy across the organization.
When approached by one of the world’s largest spice manufactures with a request to design an automated labeling solution to improve productivity, LabelPack Automation came up with a winning design.
The Problem – Manual Labeling Is Not Efficient.
The spice company had multiple locations and had major concerns about their labeling process.
The company was concerned about inaccuracies in the label data, mismatches of labeled containers during production and the general inefficient nature of their labeling process. These problems presented potentially devastating consequences for the company in the food & beverage industry.
With their current labeling system, one shift would print labels and apply them to spice bags in bulk based on a “best guess” for the following day’s production. The following shift was then responsible for filling the product into the pre-labeled bags. However, the organization found that with this process they were constantly at risk for:
- Material waste – Too many bags were labeled in the batch
- Product waste - Not enough bags were labeled in the batch
- Labeling inaccuracies – A facility could print labels with outdated ingredients which could result in potential recalls.
The spice company’s pressing needs included an accurate labeling solution across the corporation, on demand labeling of products, improved efficiency and a labeling solution that was cost effective.
Additionally, the customer revealed that they were planning a major migration to an enterprise-wide ERP system in the future. This meant that the labeling system designed by LabelPack would have to be easily integrated with the company’s new, selected platform – SAP.
After conducting a walk-through of the facility, follow-up meetings, and conference calls to learn more about the company and discuss possible solutions, LPA developed a system for the client that would solve the major concerns presented by the organization.
The Solution – Standardized Labeling Process
LabelPack Automation developed a solution that would label products on-demand and pull data from a centralized location to ensure consistency and accuracy across the organization’s multiple locations. The Standardized Labeling Process was implemented in the company’s 4 locations within a year. By the end of the first year, the spice company returned triple on their initial investment.
The labeling solution included four distinct components:
- Central, Corporate Database
- Centralized Label Formats
- Operator Interface
- Local PC
- Print & Apply Labeling Systems
The centralized corporate database was the data storage center for labels across the company. This database stored label formats and data such as – ingredients, product definitions, barcodes, and warning labels. If data on a label needed to be changed, it was changed in one location. Each center would access labels as needed based on production. The database was the foundation of the entire solution, and once the database was completed, LabelPack was able to design the remaining three components.
The operator-friendly, user interface controlled each automated labeling system. Once the operator selected the appropriate label to print for the production run, the local PC would request the label format from the centralized database. Any local specific batch information could also be added to the label and applied to bags of spices on demand.
The LabelPack Automation printer applicators were installed with Zebra PAX3 thermal print engines for printing and applying labels to the spice bags. Labels were fed to a vacuum pad mounted on a tamp cylinder. Once triggered, the cylinder would fire downward, pressing the vacuum pad against the bag to apply the label.
By standardizing the labeling process across the entire organization, the company was able to improve efficiency and reduce costs by streamlining supplies purchasing and parts ordering. Because label formats were stored in one location, there was no risk of branch facilities printing outdated labels with inaccurate information on them.
After the system was rolled out across the organization, the company had a 67% ROI on their investment in the first year.
About Label Pack Automation
LabelPack Automation is an expert in the design and integration of custom labeling solutions in a variety of industries. Our solutions have been implemented in many different production lines to increase throughput, reduce costs, and drive results. LabelPack sales representatives and engineers are experienced in developing solutions for the pharmaceutical and food & beverage industries as well as providing a steady flow of supplies for mission-critical applications. Our labels are FDA, Pharma, and OSHA compliant. Contact LabelPack today and speak with a sales representative to learn how LabelPack Automation can help you achieve your business goals.
If this is a system you would be interested in, contact LabelPack Automation today and speak with a sales representative.